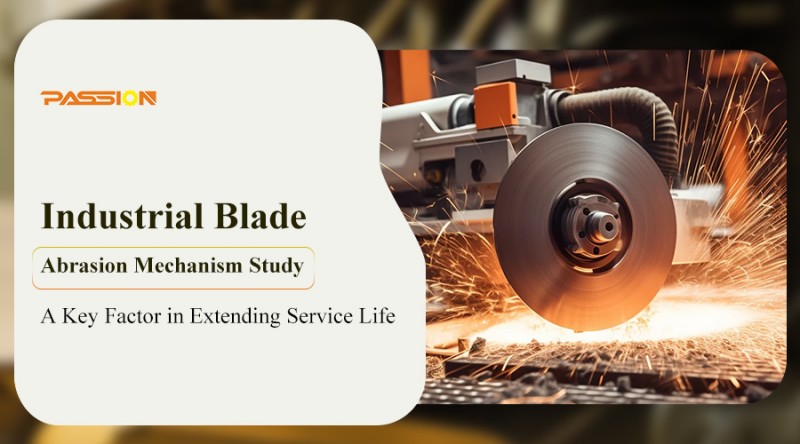
У галіне прамысловага вытворчасці ізаляцыя ляза заўсёды была важным фактарам, які ўплывае на прадукцыйнасць і якасць прадукцыі. З прагрэсам навукі і тэхналогій і пастаяннай аптымізацыі працэсу, даследаванне напрамысловае лязоМеханізм ізаляцыі становіцца ўсё больш паглыбленым, імкнучыся знайсці ключавыя фактары для пашырэння тэрміну службы ляза.

Існуюць розныя прычыны ізаляцыі ляза, у асноўным у тым ліку механічнага зносу, цеплавога зносу, хімічнага зносу і дыфузійнага зносу. Механічная ізаляцыя ў асноўным выклікана цвёрдымі часціцамі ў матэрыяле нарыхтоўкі для вырабу пазы на паверхню ляза, і такая рамка асабліва відавочная пры рэзанні з нізкімі хуткасцямі. Цеплавая ізаляцыя звязана з вялікай колькасцю цяпла, які ўтвараецца падчас працэсу рэзкі, што прыводзіць да пластычнай дэфармацыі ізаляцыі ляза або цеплавых расколін. Хімічны знос - гэта кісларод у паветры пры высокіх тэмпературах і хімічная рэакцыя матэрыялу ляза, утварэнне злучэнняў нізкай цвёрдасці, чыпа, што прыводзіць да ізаляцыі ляза. З іншага боку, дыфузійная ізаляцыя заключаецца ў тым, што падчас працэсу рэзкі хімічныя элементы на кантактнай паверхні нарыхтоўкі і ізаляцыя ляза дыфундуюць адзін з адным у цвёрдым стане, змяняючы кампазіцыйную структуру ляза і робячы яго паверхневы пласт далікатным.
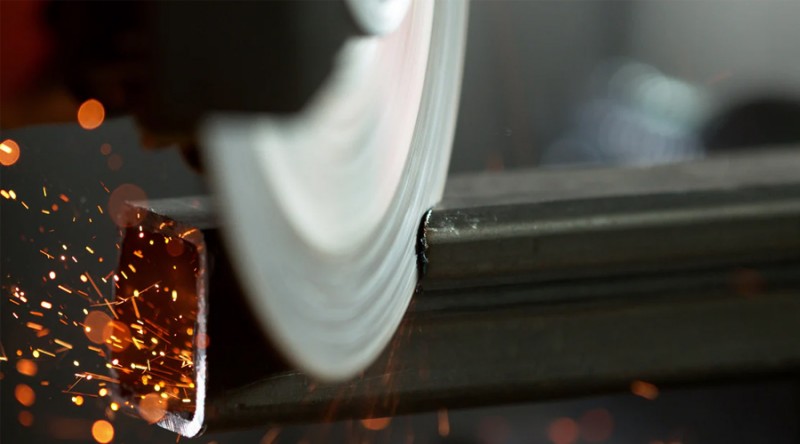
Для гэтых механізмаў зносу даследчыкі прапанавалі мноства метадаў пашырэння тэрміну службы ізаляцыі ляза. Перш за ўсё, ключавы выбар матэрыялаў ляза. У адпаведнасці з характарыстыкамі апрацаванага матэрыялу і ўмоў рэзкі, выбар матэрыялу ляза з дастатковай цвёрдасцю, зносу і трываласці можа эфектыўна знізіць ізаляцыю. Напрыклад, пры апрацоўцы складаных для выразання матэрыялаў з вялікай тэндэнцыяй да зацвярдзення трэба выбіраць матэрыял ляза з моцнай устойлівасцю да халоднай зваркі і моцнай устойлівасці да дыфузіі.
Па -другое, аптымізацыя параметраў геаметрыі ляза таксама з'яўляецца важным сродкам пашырэння тэрміну службы. Разумны кут ляза і форма ляза могуць паменшыць рэжучую сілу і разрэзаць цяпло, а таксама паменшыць ізаляцыю ляза. Напрыклад, адпаведнае зніжэнне кутоў пярэдняга і задняга і выкарыстання большага адмоўнага нахілу краю можа паменшыць знос пярэдняга краю. У той жа час, шліфаванне адмоўнай фашы або дугі краю таксама можа павысіць трываласць кончыка ляза і прадухіліць сколы.
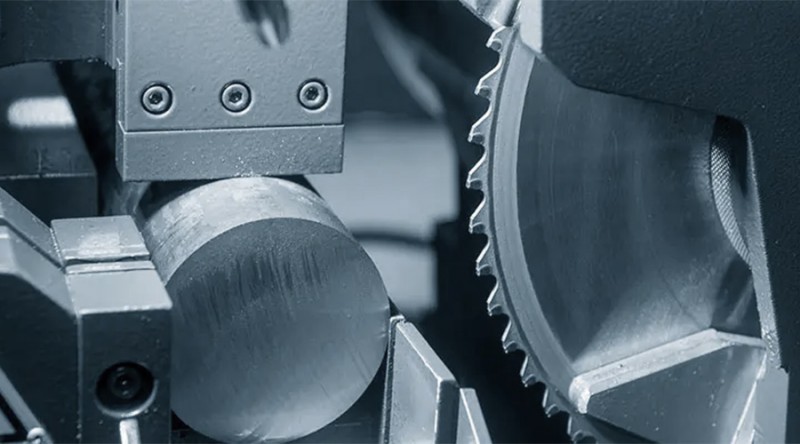
Акрамя таго, разумны выбар рэжучай дазоўкі і выкарыстанне астуджальнай змазкі таксама з'яўляецца эфектыўным спосабам падоўжыць тэрмін службы ляза. Глыбіня разрэзу і падачы занадта вялікая, сіла рэзкі павялічваецца, а ізаляцыя ляза паскораецца. Такім чынам, пад перадумовай забеспячэння эфектыўнасці апрацоўкі павінна быць зведзена зведзена колькасць рэзкі. У той жа час выкарыстанне астуджальных змазачных рэчываў можа паглынаць і забраць большую частку цяпла ў зоне рэзкі, палепшыць умовы рассейвання цяпла, знізіць тэмпературу рэзкі ляза і нарыхтоўку, зніжаючы тым самым абрашэнне ляза.
Нарэшце, правільны метад працы і калянасць сістэмы працэсу таксама з'яўляюцца фактарамі, якія нельга ігнараваць. У працэсе рэзкі лязо павінна паспрабаваць прымусіць лязо не пераносіць і менш раптоўную змену нагрузкі, каб пазбегнуць ляза з -за нераўнамернай сілы і паломкі. У той жа час, каб пераканацца, што ў сістэме працэсу добрай калянасці, памяншэнне вібрацыі таксама можа эфектыўна пашырыць тэрмін службы ляза.
Такім чынам, ключавыя фактары для пашырэння тэрміну службы прамысловых устаўкі ўключаюць разумны выбар матэрыялаў ляза, аптымізацыя параметраў геаметрыі ляза, разумны выбар дазоўкі, выкарыстанне астуджальных змазак і правільныя метады працы і калянасць сістэмы. З пастаянным паглыбленнем даследаванняў па механізме ізаляцыі ляза лічыцца, што ў будучыні з'явяцца больш інавацыйныя тэхналогіі і метады, увядзенне новай жыццёвай сілы ў развіццё прамысловага вытворчага поля.
Пазней мы будзем працягваць абнаўляць інфармацыю, і вы зможаце знайсці больш інфармацыі ў нашым блогу (PassionTool.com).
Вядома, вы таксама можаце звярнуць увагу на нашы афіцыйныя сацыяльныя медыя:
Час паведамлення: лістапад-15-2024